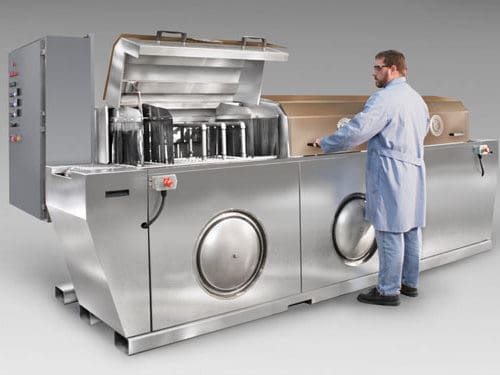
Remove Hardened Resin from 3D Printed Parts
This company manufactures high-performance products for high-technology companies, government agencies, and academic institutions. One of the products they manufacture in particular is ceramic turbine blade castings for the aerospace industry. For this reason, lithographic etching and CNC machining combine to produce master patterns and high-resolution lithographic inserts for these highly complex three-dimensional parts.
Parts Cleaning Challenge
The process begins with 3D printing the model in a wax-like resin. This resin hardens on the molds and is difficult to remove. As a result, the challenge was to remove hardened resin from the ceramic turbine blade molds.
Solution/System
In this case, the solution was a Cyberjet conveyor washer with a 14” wide belt with a recirculated spray wash and two recirculated spray rinse zones. A temperature of at least 165° F has to be maintained, the wash tanks and rinse tanks were increased to 225 gallons each, and the heater elements increased to 27 kW in order to remove the hardened resin. The throughput is one fixture of parts every 8 minutes, and pusher bars were affixed to the belt to help maintain a specific distance in the center of each module.
In addition, a wax removal basket and containment divider was designed for every stage. The system also included marine cleanout doors for both the wash and rinse stages for easy maintenance. A steam containment door was installed at the exit side of the machine instead of spray curtains to limit the amount of time steam can escape from the unit. Altogether, this type of system worked well as this was an indexing unit, loaded and unloaded robotically. The system also featured:
- Allen Bradley CompactLogix PLC and Panelview
- variable frequency drive controls
- water level controls
- locking lid safety switches
- safety guarding on the load and unload ends to cover bearings and sprockets
- electronic pressure switches
- in-line bag filters
- insulation for the entire system
Please contact us to learn about more cleaning applications like this!