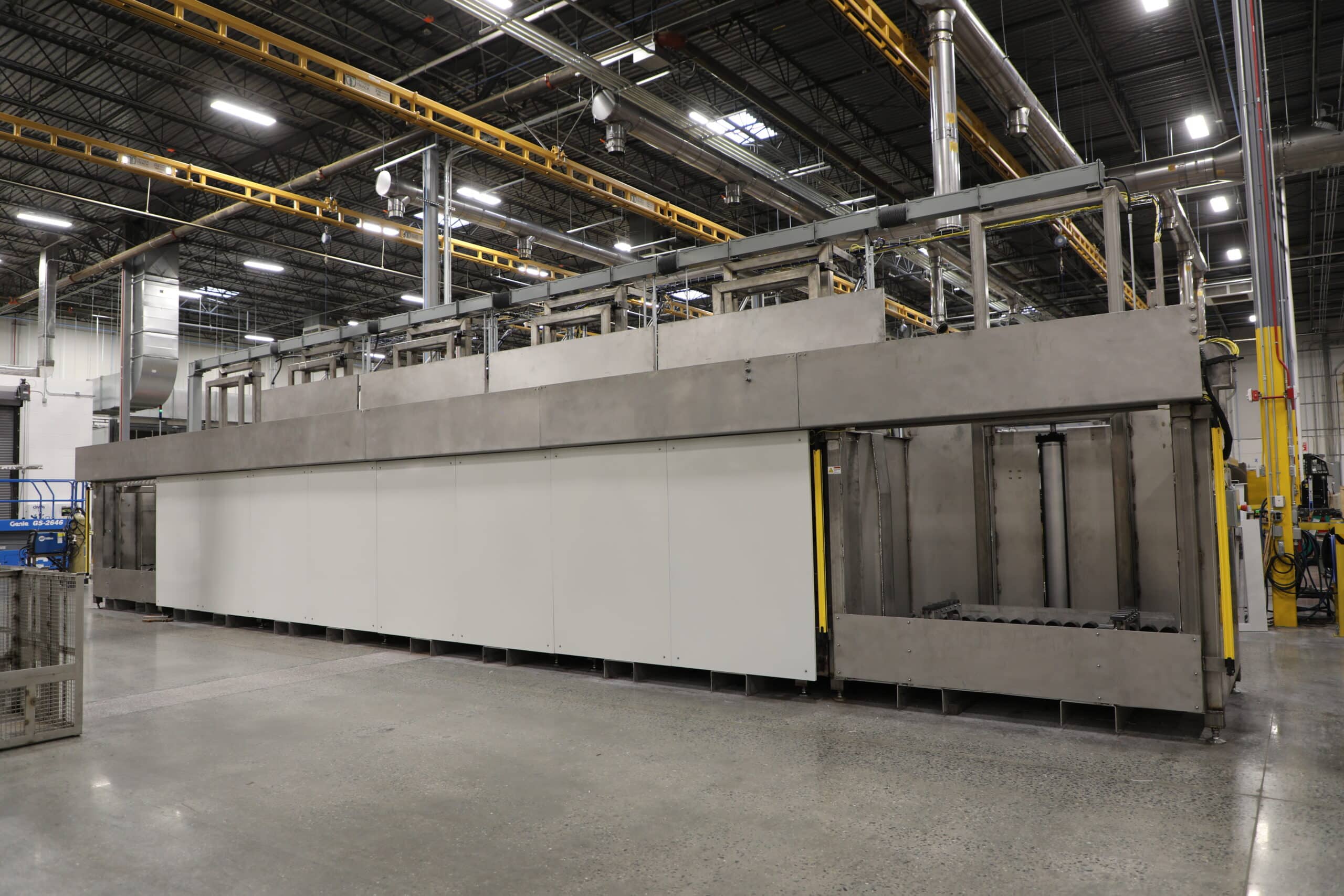
Large Automated Immersion Washing System to Clean Aluminum Parts – Case Study 23383
Brief This company is a relatively large aerospace sheet metal contractor with multiple facilities throughout the US. They produce high-end welding for titanium–sheet metal on jet engine nacelle rings. …