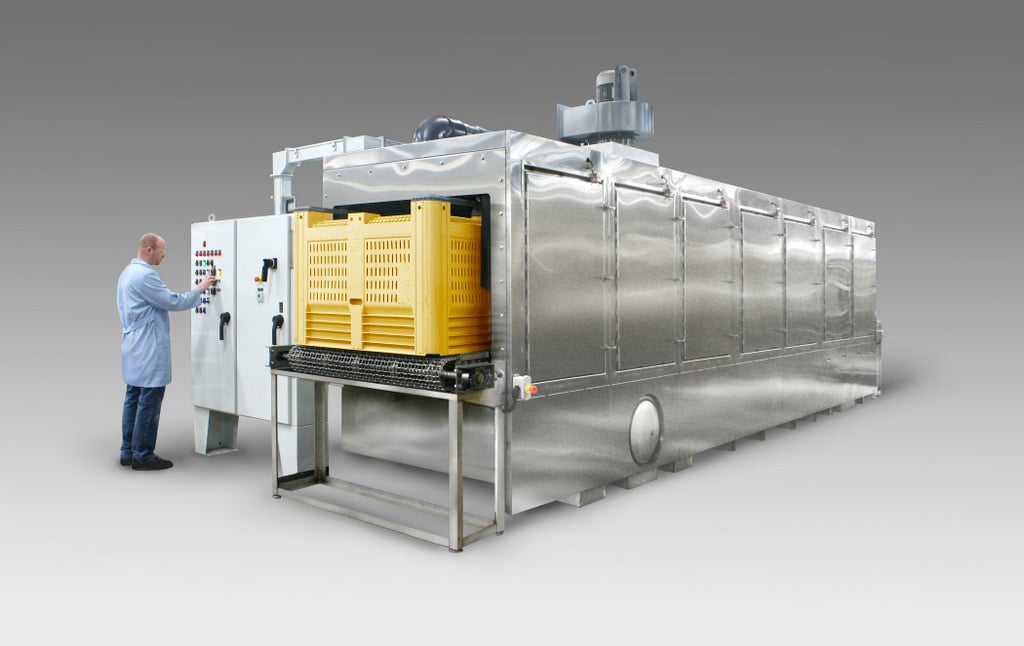
Effective Agriculture Hygiene Solutions: The Power of Sanitization Tray Washers
Bird flu remains a formidable challenge for the agricultural sector, posing significant threats to poultry farms and food supply chains. Implementing rigorous biosecurity measures is essential for mitigating the risks …