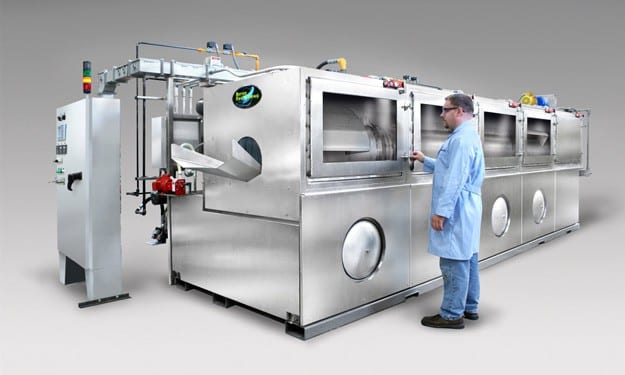
Small Ammunition Cleaning – Case Study 21130
Cleaning Small Ammunition Casings After Heat Treatment Background: Cleaning small ammunition casings is imperative after heat treatment to remove chips and cutting oils in manufacturing to achieve optimal product …