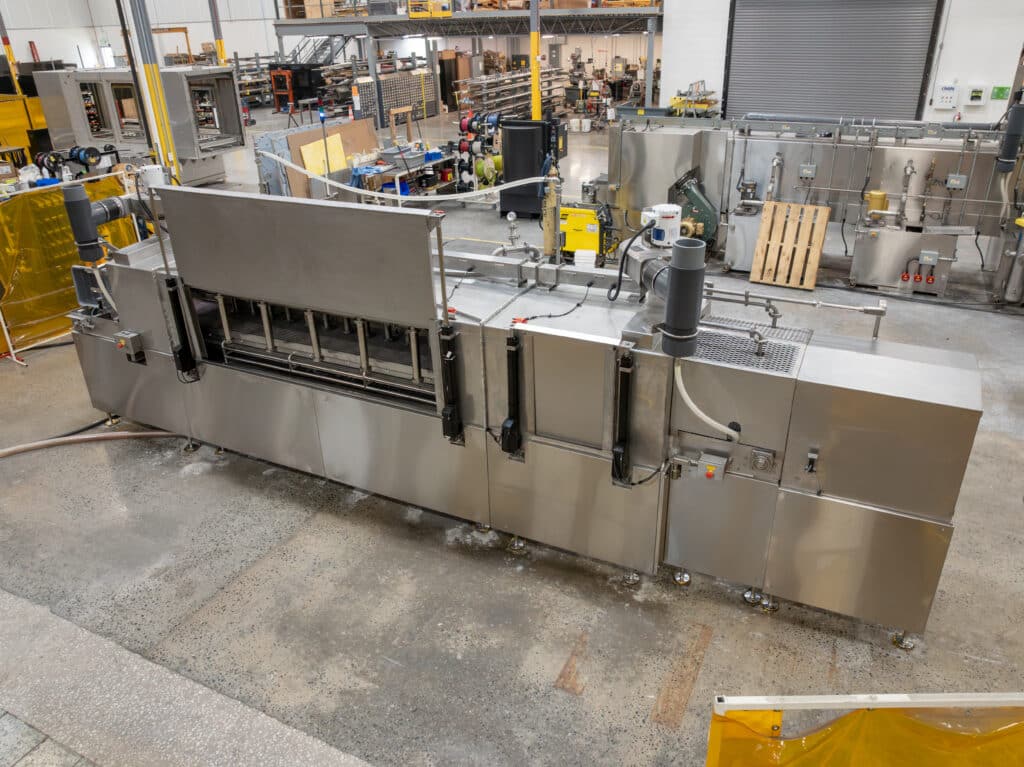
Brief
Before partnering with Better Engineering (BE), the customer was manually washing 30 plastic luggers per hour, resulting in significant water and detergent wastage. Seeking a more efficient and sustainable sanitizing tote solution, they turned to BE to enhance their cleaning process and throughput. Post-installation, they aimed to increase their washing capacity to 130 luggers per hour.
Approach
Better Engineering distinguished itself through a meticulous approach to understanding and addressing the customer’s needs. The process began with a comprehensive analysis of the customer’s current operations, followed by extensive testing to validate the proposed system’s performance. This rigorous evaluation included ATP (Adenosine Triphosphate) testing, a scientific method used to measure cleanliness levels accurately. By conducting these tests, BE ensured that their solution would not only meet but exceed the customer’s stringent cleanliness standards.
Working within the customer’s specified footprint of 20 feet, BE designed a state-of-the-art food processing container washer for sanitizing totes tailored to the customer’s unique requirements. The machine incorporates several innovative features:
- An 18-inch fresh rinse zone operating at a high temperature of 180°F, enabling effective sanitization using only hot water without additional chemicals
- A fully washdown-rated system, ensuring durability and ease of maintenance
- An 8-foot wash zone for thorough cleaning
Advanced Features and Benefits
The food processing container washer designed by BE offers several advanced features that significantly enhance the cleaning process:
- Water Recirculation and Filtration: The system incorporates a sophisticated water management system that recirculates and filters water, dramatically reducing overall water consumption.
- Chemical-Free Sanitization: By utilizing high-temperature water at 180°F, the system eliminates the need for additional sanitizing chemicals, promoting a more environmentally friendly cleaning process.
- Automated Processes: The machine’s automated design significantly reduces the need for manual labor, cutting labor costs by approximately 50%.
- Vertical Powered Maintenance Doors: This feature enhances accessibility for maintenance and cleaning, improving overall operational efficiency.
- Dual Lane Processing: The system is equipped with separate lanes for processing lids and totes simultaneously, further boosting throughput and efficiency.
Conclusion
The collaboration between the customer and Better Engineering resulted in a transformative solution that far exceeded initial expectations. By implementing BE’s innovative sanitizing tote washer, the customer achieved remarkable improvements in their cleaning process:
- Increased cleaning capacity from 30 to 130 luggers per hour
- Significant reduction in water usage through recirculation and filtration
- Elimination of sanitizing chemicals, promoting a more sustainable operation
- 50% reduction in labor costs due to automation and efficient design
This comprehensive solution not only met the customer’s immediate needs but also positioned them for long-term success in terms of efficiency, sustainability, and cost-effectiveness. The project stands as a testament to Better Engineering’s commitment to innovation, customer satisfaction, and environmental responsibility in industrial cleaning solutions.
Interested in finding your solution? Contact us for more information, a facility tour, or free part testing.