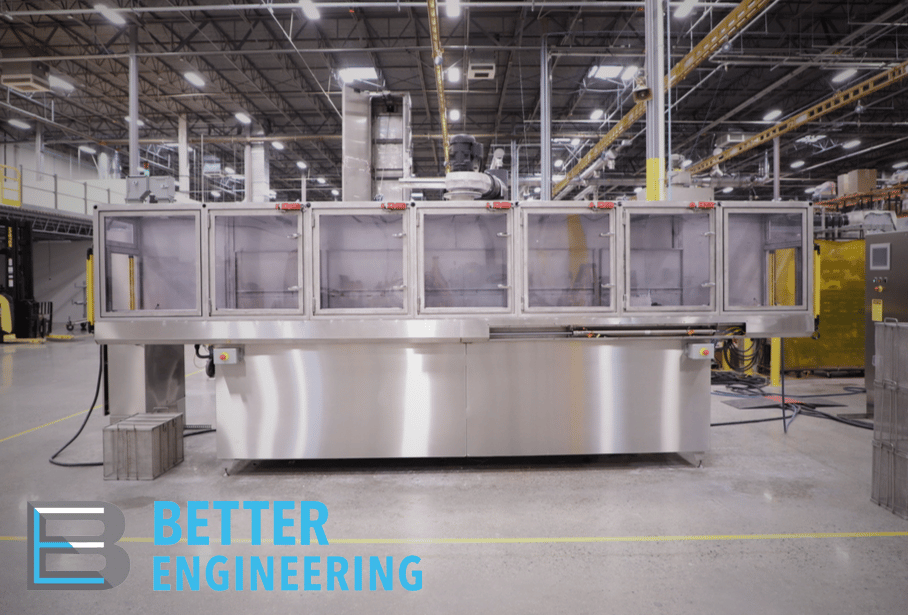
What is Metal Preparation and Passivation?
What is Metal Preparation and Passivation? Metal preparation and passivation is the critical surface-finishing process for steel. Stainless steel is undoubtedly one of the world’s most versatile and widely used …