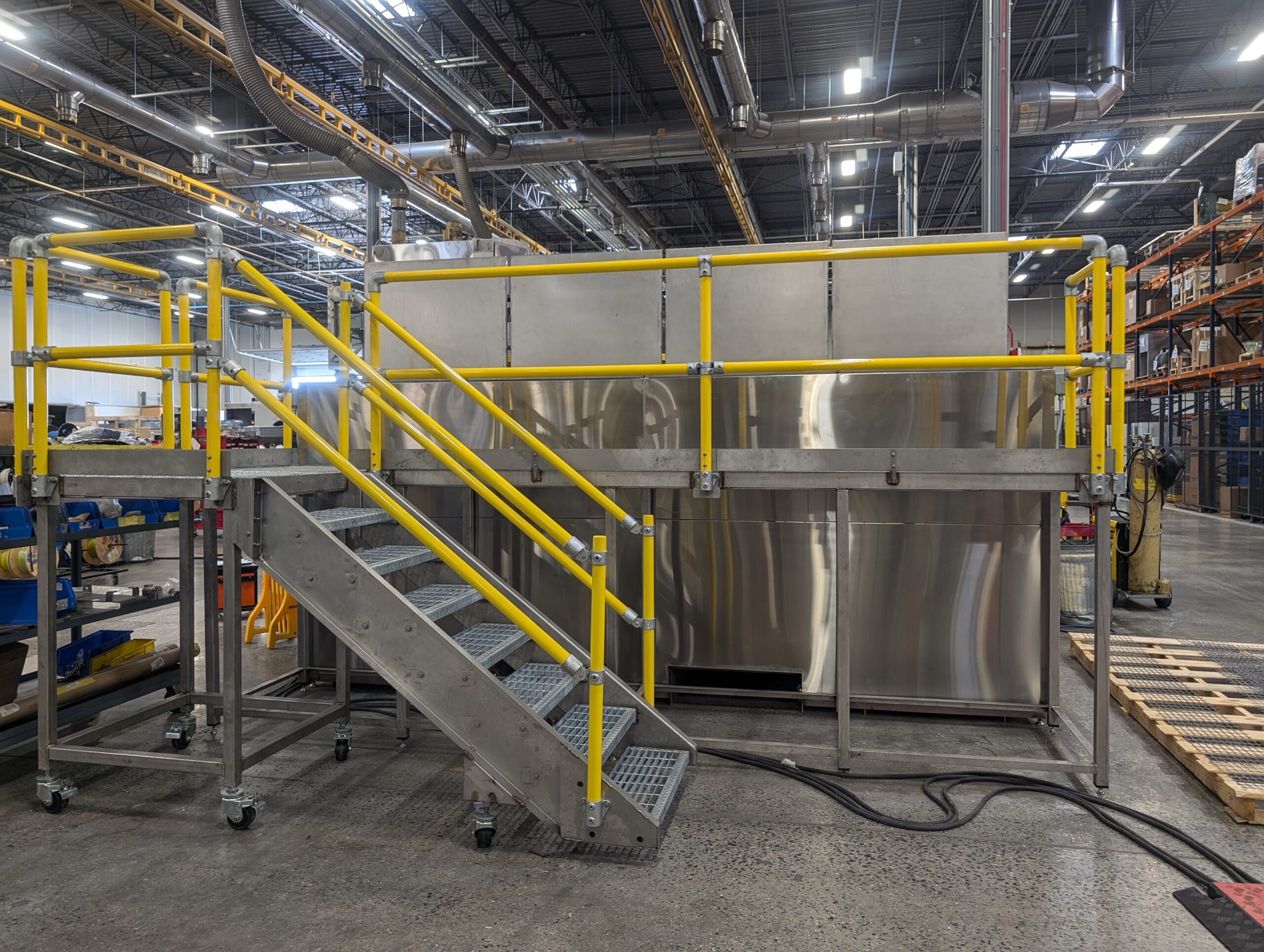
Industrial Immersion Washer for Caterpillar Engine Component Racks – SN 23825
Challenge A leading Caterpillar engine rebuilder in the Western U.S. faced a significant operational challenge: efficiently cleaning heavy-duty Caterpillar engine components such as nuts and bolts, stacked in large steel …