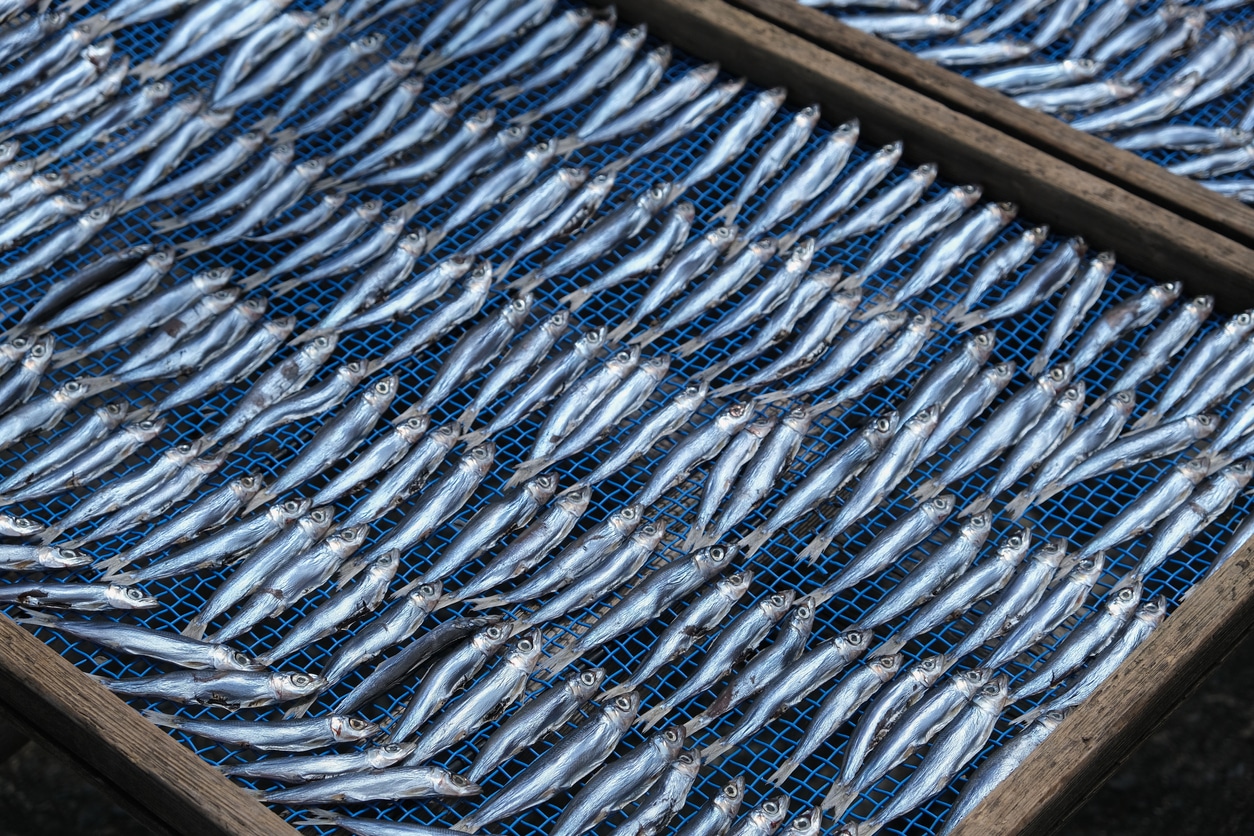
Sink or Swim: The Importance of Washing Metal Racks in Seafood Processing Facilities
Washing metal racks is essential to maintaining a clean and efficient fish processing facility. With constant exposure to salt and other contaminants, these racks can quickly become corroded and harbor …