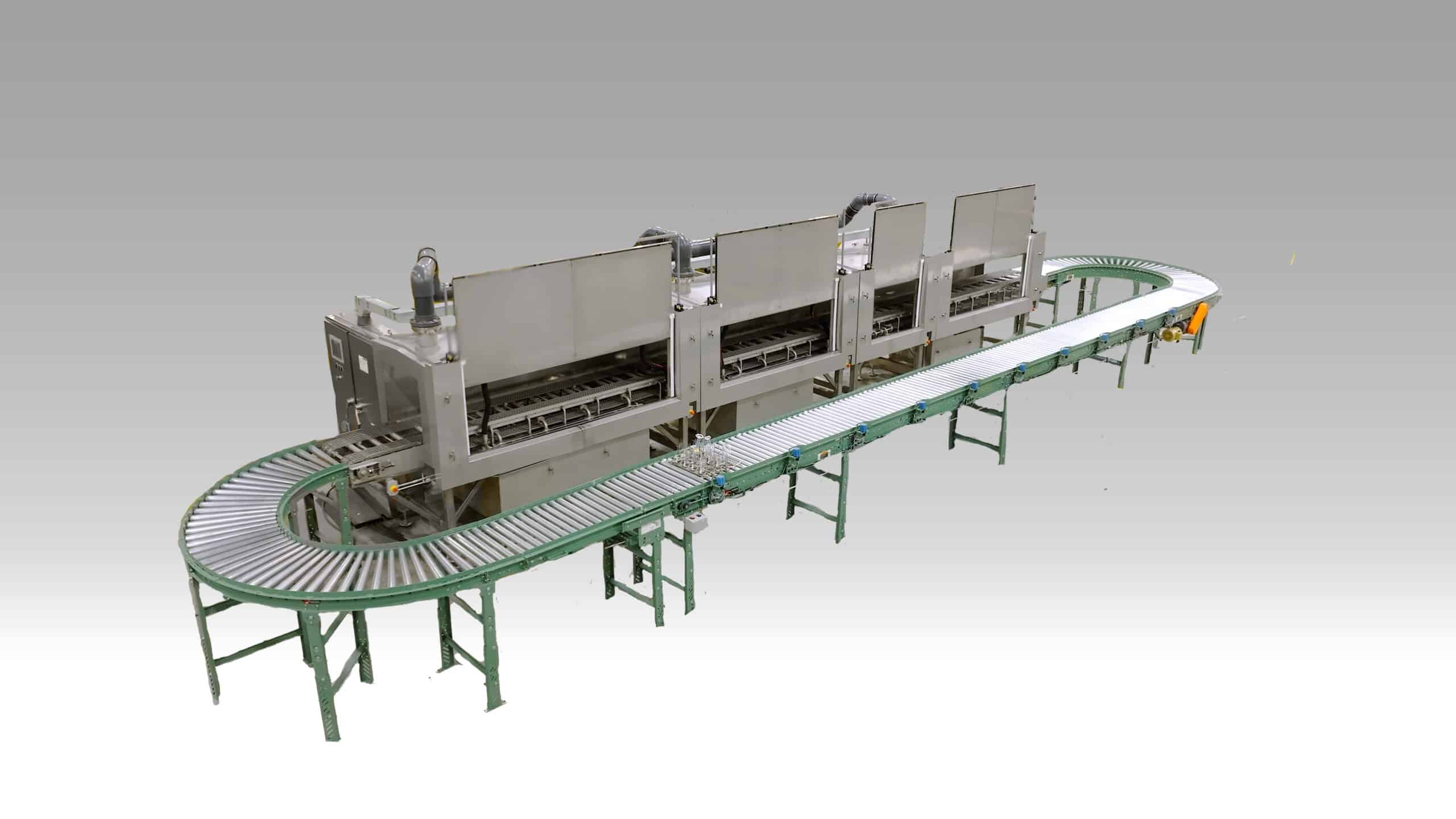
Understanding Washdown Ratings and Washdown Compatible Machines
When selecting machinery and equipment for an industrial operation, it is vital to consider the environment in which they will be used. Many machines must withstand frequent washdowns or be …