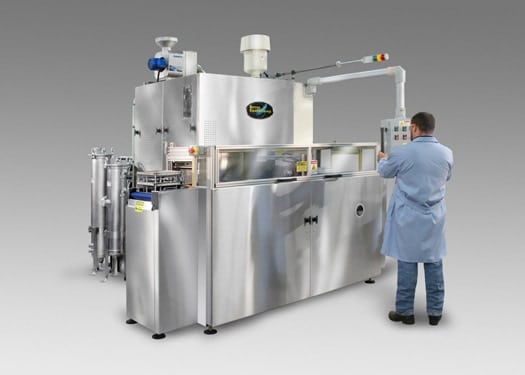
Fuel Injector Parts Cleaning – Case Study 21780
Automatic Fuel Injector Parts Cleaning Background This company is a leading manufacturer of automotive air conditioning and engine cooling components and systems. Part of their manufacturing process requires fuel …