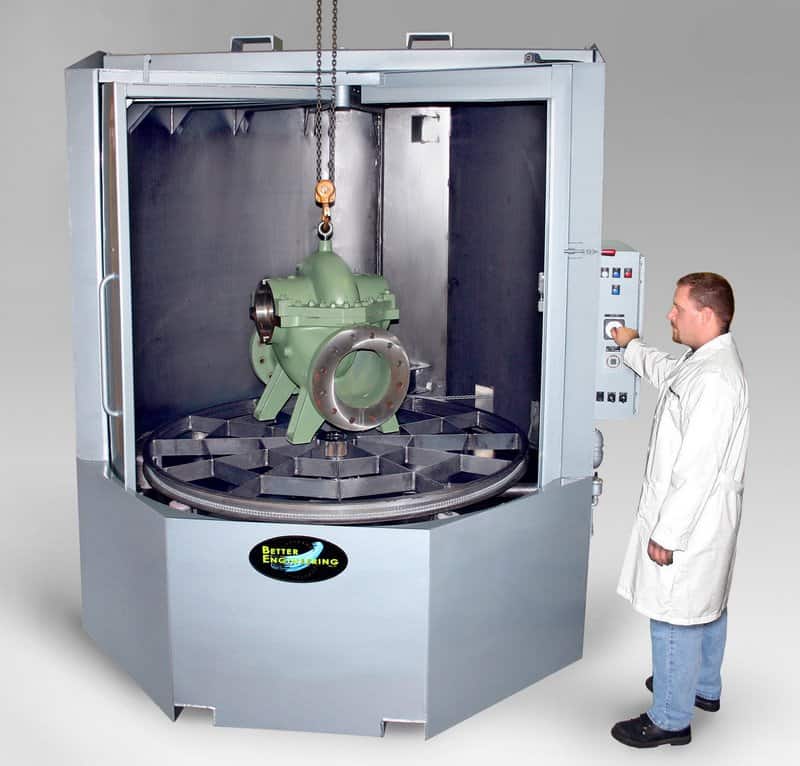
Spray Washer for Large Castings – Case Study 20700
Spray Washer for Large Castings Background: This family-owned, 80-year old company manufactures components for industrial hot and cold water circulation systems: pumps, valves, heat exchanges, air removal devices, etc. …