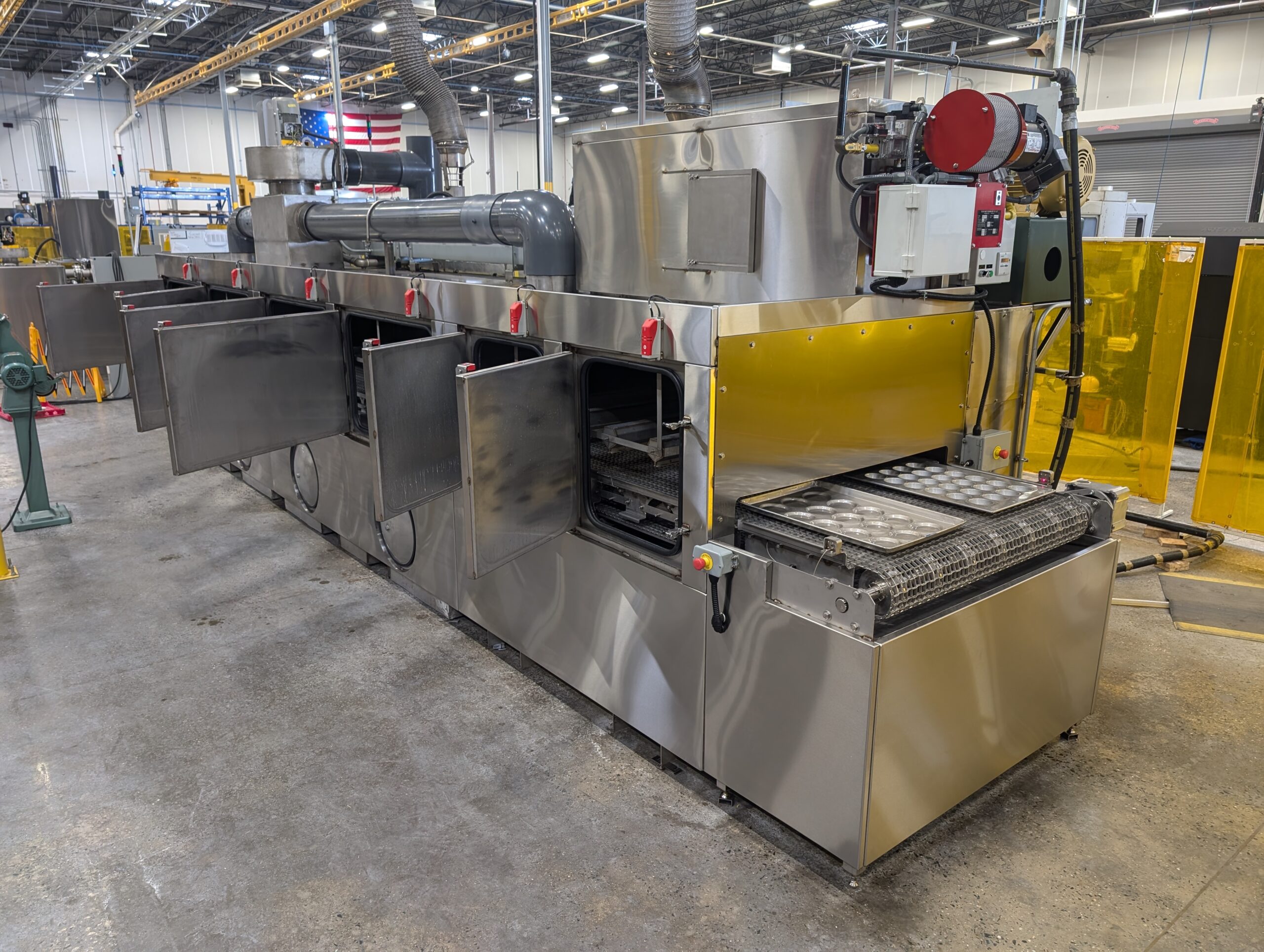
Tunnel Tote washer for Snack Food Processor – SN 23809
Challenge A leading snack food processor required a tunnel washer solution to keep pace with their high-volume production demands. The system needed to hygienically clean a wide range of reusable …